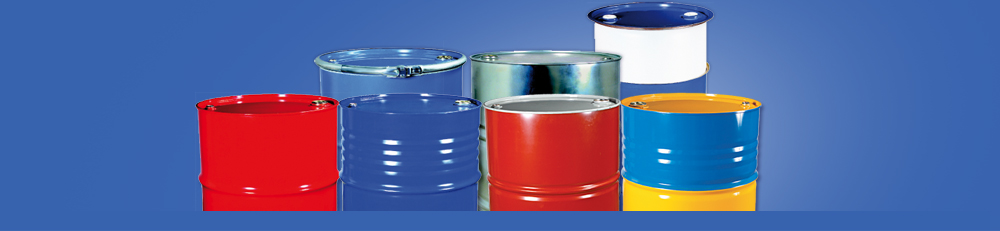
Product / Product Feature

Controlled automatic guns are used for applying seaming compounds for uniform application and minimum wastage. Reduces chance of contact of seaming compounds with filled in product. High quality seaming compound used with high degree of chemical resistance.

Fully automatic internal and external degreasing plant is an on-line process. Each drum on-line is cleaned both internally and externally and treated to maintain clean surface and prevent rusting. Surface preparation facilitates excellent painting as well as internal coating as applicable.
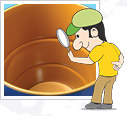

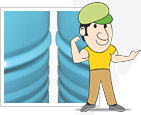
Specially profiled '1A/' shaped rolling hoop formed by corrugation below and above the rolling hoop which is positioned slightly inside. It provides additional rigidity (vacuum resistance) and imparts greater stacking strength. Unique profile prevents hoops protruding unlike conventional drums from fouling with each other and consuming larger stacking space. 4 drums can easily be stacked side by side in a shipping container. Reduced chances of paint peeling off due to the hoops not rubbing against each other. Enough protrusion to aid rolling of drums on hoops and protect printing/ labels on the side body.

Offers higher resilience even to lightweight drums

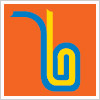
Specially compressed triple seam construction guarantees complete integrity and sealing of the drum ensuring no leakage.

Sophisticated painting system ensures uniform & high gloss painting. Integrated microprocessor controlled baking oven guarantees uniform and reliable curing of pure stowing enamel paint, resisting chipping off / abrasion during transit. Specialised V-axis painting enables painting of seams as well.

Glossy screen printing is done on automatic high speed screen printing machine for consistent & uniform printing.

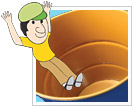
Drums are internally coated with epoxy/ lacquer using sophisticated spraying guns for uniform application. Drums are pretreated to facilitate good quality coating and a sophisticated baking process is adopted.